Roller coasters—the very phrase conjures images of twisting tracks, screaming riders, and that anticipation as you crest the first hill.
But what’s really behind these engineering marvels?
How do manufacturers turn raw materials into the steel giants and wooden legends that pack parks with thrill-seekers every season?
This is your ultimate guide to roller coaster construction:
Materials, techniques, safety secrets, and more.
The Building Blocks: Materials That Shape the Ride
Let’s not sugarcoat it: your choice of material can make or break a roller coaster.
Through decades of trial and error, two materials have emerged as the clear favourites—wood and steel.
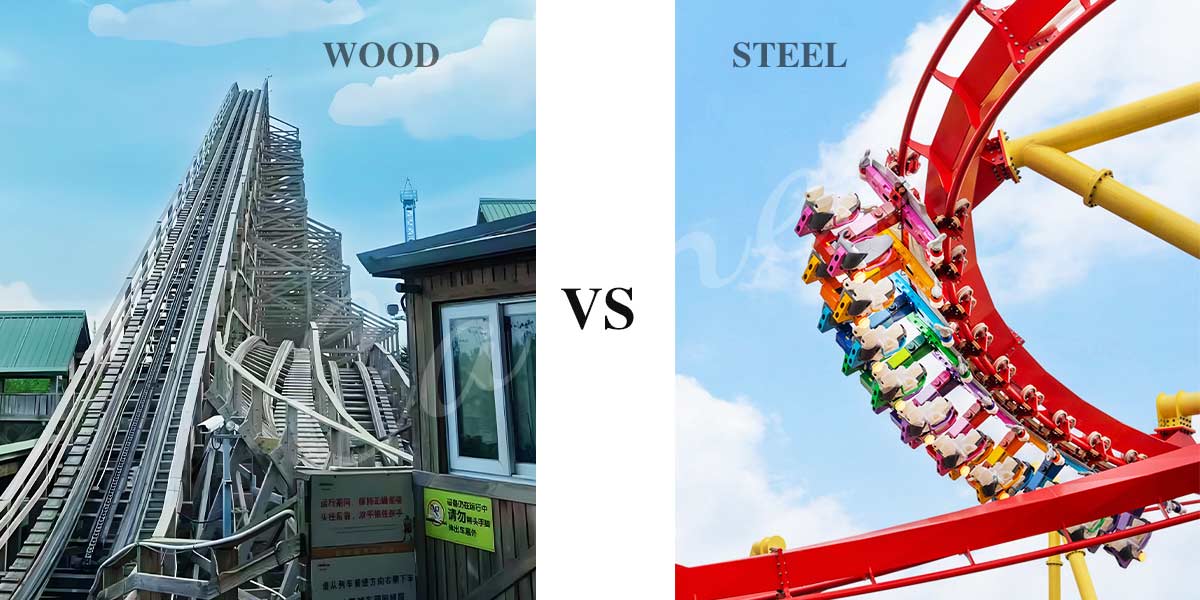
Wood: The Classic Choice
Wooden coasters bring a nostalgic thrill you just can’t replicate with anything else.
They creak, they sway, and every ride feels unique.
Key Features:
- Materials: Southern yellow pine and Douglas fir—tough, flexible, reliable.
- Structure: Latticework of wooden beams, secured with steel bolts and plates for stability.
- Track: Laminated wood strips, topped with steel rails for smoother rides and less wear.
Downsides?
Wood needs ongoing maintenance—watching for rot, warping, and weather damage.
But for many parks, the classic feel is absolutely worth it.
Steel: The Modern Marvel
Steel coasters changed the game.
Suddenly, loops, corkscrews, and wild inversions became possible.
Designs are almost limitless.
Features of Steel Roller Coasters:
- Materials: Tubular steel, structural steel beams, reinforced concrete.
- Track: Factory-welded steel tubes, bent for seamless twists and turns.
- Supports: Usually steel, sometimes concrete, giving strength without bulk.
Steel lets you dream big—bigger, faster, crazier.
But don’t be fooled, they need strict inspections and regular maintenance, too.
Want more details?
Check out AZoM’s roller coaster material guide
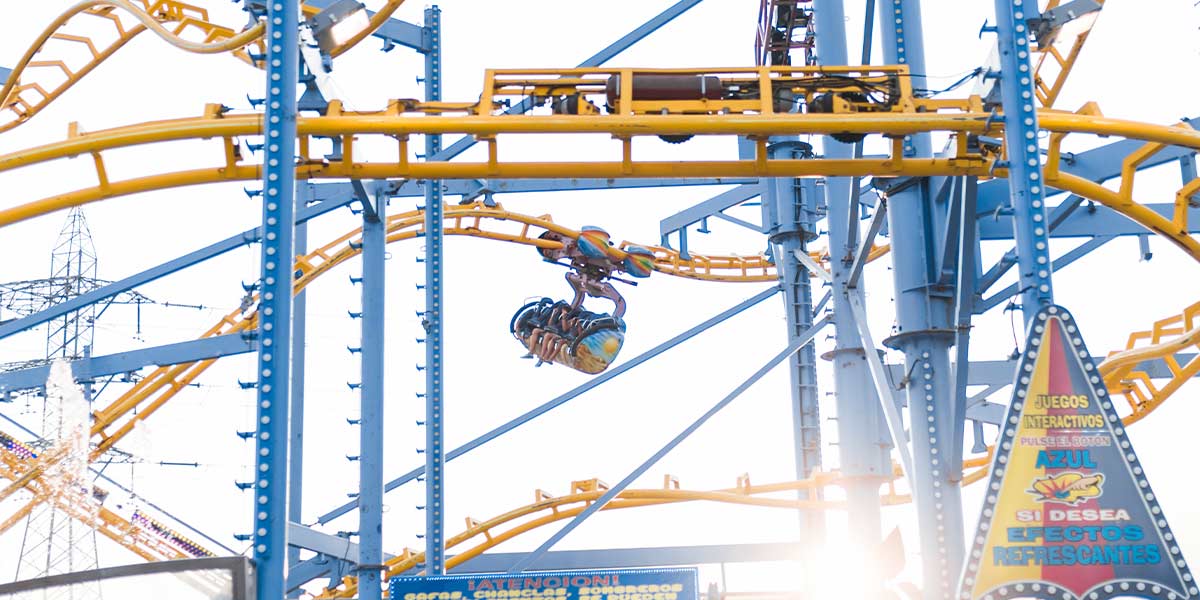
Construction Techniques: From Blueprint to Scream Machine
Building a coaster isn’t a DIY job.
It’s a massive team effort—from engineers and fabricators to skilled construction crews.
The typical construction process looks like this:
1. Design and Engineering
- Computer modelling, simulations, and calculations for safety and thrill
- Engineers calculate every force, load, and clearance
Want to see how different coaster types influence design and ride experience?
Our easy guide and comparison chart of roller coaster types breaks it all down.
2. Fabrication
- Tracks and supports are manufactured off-site for maximum precision
- Steel tracks are welded and shaped in factories
- Wooden beams cut and treated for longevity
3. Site Preparation
- Massive concrete foundations poured
- Groundwork and utilities installed
4. Assembly
- Supports are erected first, then the track sections go up
- Cranes and specialist rigs handle heavy, high-precision lifting
5. Final Touches
- Cars, lift chains, brakes, and safety systems installed
- Every system is tested and checked before public runs
Behind-the-Scenes Techniques
- Prefabrication: Factory-building sections means fewer weather delays and better quality.
- Modular Assembly: Track comes in sections for easier shipping and faster onsite builds.
- Laser Alignment: Laser tech ensures each piece fits perfectly—no bumps, no surprises.
Modern coasters demand precision equal to skyscraper construction.
Want proof? Just look at the innovation and trends in The Ultimate Guide to Roller Coasters in 2025.
Safety First: Engineering Reliability Into Every Ride
Ever stood in line and wondered, “How safe is this coaster?”
You’re not alone.
Safety is engineered into every aspect:
- Redundant restraint systems: Harnesses, belts, lap bars—all checked and double-checked.
- Regular inspections: Daily walk-throughs, monthly overhauls, yearly shutdowns for deep maintenance.
- Automated control systems: Computers monitor speed, position, and brakes in real time.
- Material testing: Every batch of wood and steel is tested for strength and durability.
Real talk:
The real heroes? Maintenance crews work before dawn and after dark to keep every bolt tight.
Looking for amazing facts about roller coaster safety records, the world’s tallest, or surprising stats?
Don’t miss our Fun Facts About Roller Coasters for more!
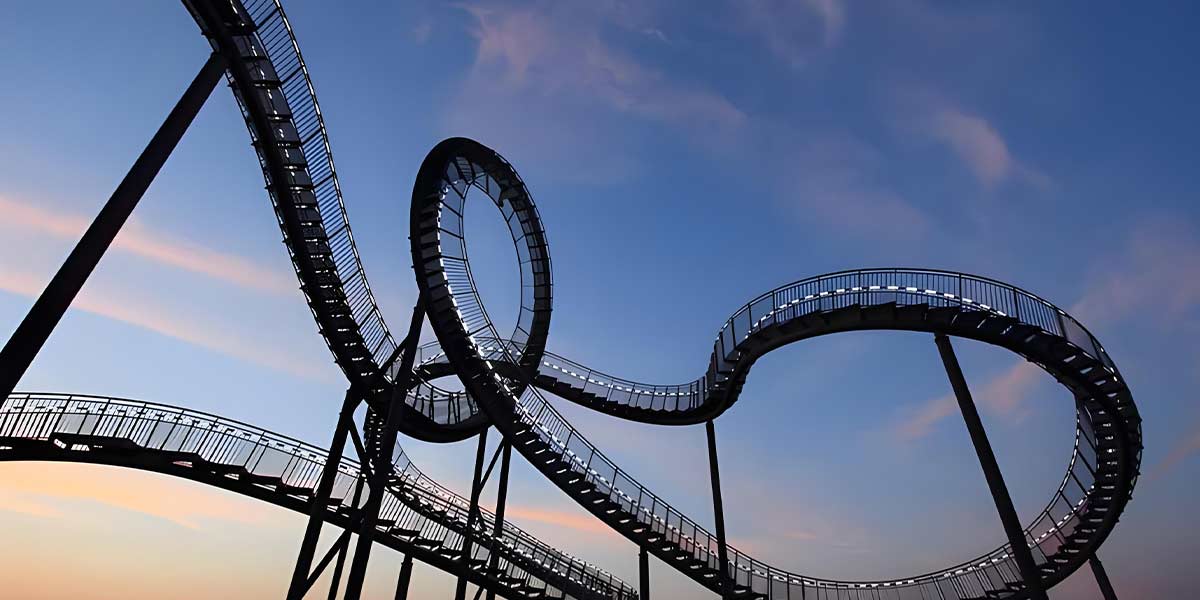
What Sets Great Roller Coaster Manufacturers Apart?
- Use of top-quality materials (certified steel, treated wood)
- Factory precision for all structural components
- Modern safety systems with digital controls
- Transparent maintenance plans and global support
- Customisation for different heights, layouts, and park themes
If your supplier can’t deliver on these, keep looking.
The Future: What’s Next for Roller Coaster Construction?
Innovation never stops.
Now we’re seeing hybrid coasters (wood+steel), magnetic launch tracks, VR integrations, and even AI-controlled rides.
The next decade?
Imagine coasters that adapt to your mood in real time—thrill on demand.
Conclusion
From material choice to final safety checks, roller coaster construction is a blend of science, engineering, and pure creativity.
Next time you strap in, remember:
Behind every scream is a world of planning, precision, and passion.